Harmonic Measurements: 6 errors that cost
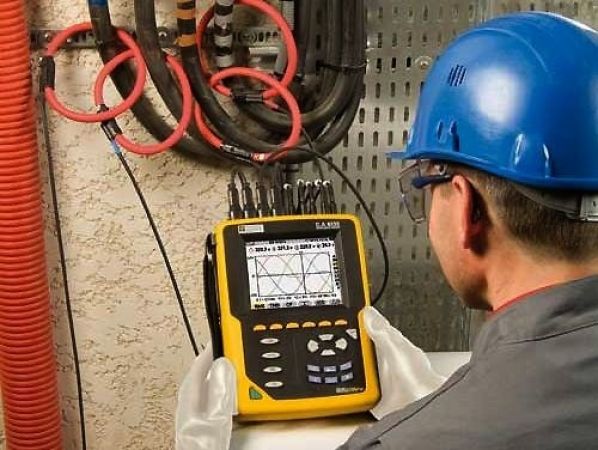
Proper and complete management of the harmonic problem requires the execution of correct and adequate measurements.
In reality, however, very serious mistakes and omissions are observed, which lead to the collection of incorrect or incomplete data and hence to the incomplete handling of the problem of harmonics.
In the worst case scenario, selective measurements are deliberately made to produce targeted results (for ex. high savings rates, major power factor correction needs, etc.) with misleading calculations to create a misleading picture of the real needs of the electrical installation and the required equipment.
The six most common errors that occur during the harmonic measurements are presented below.
Error 1: Improper measurement equipment
The first and most important requirement for proper harmonic measurements is the use of the appropriate equipment.
It is often noticed (either from ignorance or by intent) that many people attempt to measure with single-phase amp-meters, voltmeters, cos-meters or low-precision energy analyzers.
None of the above methods is a correct measurement of harmonics.
In order to measure the harmonics, three-phase energy analyzers with a high degree of accuracy are required.
But why are three-phase energy analyzers the necessary equipment for electrical measurements?
Firstly, because three-phase energy analyzers are the only devices that can measure all the relative values (voltages, currents, powers, harmonics, etc.).
Secondly, because three-phase energy analyzers have the ability to record data for a long time, a prerequisite for obtaining sufficient data.
Nevertheless, you should be aware that three-phase energy analyzers used for harmonic measurements should meet the requirements of the international standard EN 50160.
Error 2: Brief time of measurements performance
The time required for performing harmonic measurements varies depending on the operating characteristics of the installation. There is a huge difference between those installations that are relatively stable and those where their operation is constantly changing.
For example, newsprint or food preservation facilities have a similar day-to-day operation, while industrial production facilities are constantly changing, depending on a number of factors such as product demand, season, weather conditions, etc.
It is pointless, for example. to perform measurements in a heavy industry during a season when it only works at 20% of its total production capacity (due to reduced demand) or on a cruise ship in spring when the air conditioning system is not used.
The usual practice for medium-sized industries is that the measurements last for about 4 days, while for the bigger-sized, the corresponding time may be weeks.
In any case, however, measurements are not to be made for a period of less than 24 hours, on a sampling basis or at times where no critical transients such as startups, shutdowns, scheduled uses of back-up generators take place.
A sufficient number of days must be devoted to complete recording and stamping of the plant’s operating cycle.
Error 3: Incorrect measurement point
Another significant error that occurs when performing harmonic measurements is the selection of the connection point of the instrument. Several technicians collect sampling measurements from different points in the network, believing that in this way they will get a more detailed picture of the installation.
However, sampling at different points in the network is an incomplete and erroneous method because it is practically impossible to carry out sampling checks on the entire plant, especially if the installation involves many different loads.
At the same time there is a risk of making serious errors in current harmonic measurements. Unlike the voltage that is constant (400V at all points on the network), the current value is not constant, as Kirchhoff’s 1st rule applies.
As shown in the following figure, if the measurement is made at (the wrong) point B, the instrument will only record the harmonic current of the particular branch and not the total, which would be recorded if the measurement was at the (correct) point A.
Image
It is now an international practice to measure the so-called PCC (Point of Common Coupling) as it is called in IEEE 519.
The Point of Common Coupling must be close to the Power Transformer and usually on the LV bus bars, as indicated in the figure above.
By this way, the power analyzer records the entire measured quantities, not a part of them.
Error 4: Missing size rating
In order to perform an adequate and sufficient measurement , EN 50160 international standard specifications must be met. EN 50160 mentions, among other things, all the necessary electrical sizes to be taken into account.
In practice, however, contrary to what the standard defines, when evaluating the harmonic measurement results, it is common practice to focus only on THDv and THDi harmonic distortion indicators.
However, for the correct evaluation of the results, the following power quality related sizes should be taken into consideration:
1. Voltage and its fluctuations
Many times the equipment failures or abnormalities in the operation of the production lines are mistakenly attributed to the existence of harmonics, and the real cause is the large fluctuations in voltage.
Why is this happening; Because only the THDv and THDi harmonic distortion indicators are taken into account and no complete measurements are made.
For example, there is the phenomenon of hypertension (where the equipment is in danger of being destroyed) and the sinking phenomenon (where the equipment is under-functioning and does not perform satisfactorily).
However, if only the THDv and THDi harmonic deformation indicators are measured, and there is no overall assessment of the state and integrated measurements, there is a risk that the problem is diagnosed as a harmonic problem, and in fact there is a voltage problem.
In this case, the purchase of harmonic filters will be proposed – wrongly – while the appropriate equipment is a voltage stabilizer.
It is obvious that the cost of purchasing and installing the wrong equipment, due to a lack of assessment of the situation and of inadequate measurements, will be very high.
2. The maximum operating voltage IL of the installation and the short circuit current Isc of the Power Transformer
As will be explained in a next paragraph, these values are particularly important for assessing the harmonic intensity.
3. The reactive power and cosine value
Harmonic and power factor correction are two interconnected concepts but are not identical concepts. In practice, however, they happen to be used as identical concepts, leading to unnecessary costs.
In particular, low cosφ value does not necessarily mean having harmonics. But if it is misinterpreted as a harmonic, then it can lead to the purchase of equipment for the elimination of harmonics, without harmonics being present!
We note, however, that there are also occasions where there is a need for both power factor correction and harmonic compensation.
In cases where there is only a need for correction of the power factor, this is usually achieved using capacitor arrays.
However, in cases where there is also a need to compensate harmonics, the capacitor arrays do not correct the problem and other solutions such as active harmonic filters must be used.
In any case, however, when performing power quality measurements, both reactive power and power factor values should be measured, provided they are not confused with those of the harmonics and are evaluated separately.
Error 5: Using wrong voltage harmonics limits
With regard to harmonics specifications, there is a great number of standards around the world, fact that creates confusion as to what are ultimately the limits one should aim to ensure in order to make sure that an installation operates safely.
The most well-known international standards of harmonics are IEEE 519, IEC 61000 and EN50160.
For years, there has been considerable variation between the limits of the aforementioned standards, as the US IEEE 519 indicated 5% THDv harmonic distortion limit, while European standards IEC 61004 and EN50160 were 8%.
However, since its latest revision in 2014, IEEE 519 also adopted 8% as a threshold for harmonic distortion, resulting in a full standardization of standards.
However, the empirical introduction of 5% as a target even today, leads many technicians wrongly to increased hedging requirements and hence demand for overdimensioned filters (always related to their actual needs), which unnecessarily increases overall purchase costs.
Error 6: Use of the wrong harmonic measurement indicator
Unlike voltage harmonics, current harmonic are often ignored.
This is mainly due to the following three reasons:
- Usually equipment failures and line breaks are more often due to voltage harmonics and less to current harmonics.
- The European standard IEC 61000 does not indicate current harmonics distortion limits except for levels up to 16A.
- Many measuring instruments do not measure the total harmonic distortion factor TDD, which is the factor that IEEE 519 standard classifies the installations according to their harmonics.
At this point, because many do not know what the TDD means and how it affects the measurements, etc., we will spend some time presenting this indicator.
What is the TDD?
The THDv factor is used to measure the voltage harmonics distortion according to the following formula.
The corresponding THDi factor is used to measure current harmonics distortion.
The two THDv and THDi factors have a very significant difference.
In the first factor, the denominator is always fixed at 380 or 400V as the installations operate at a constant voltage.
In the second factor, however, the denominator is constantly changing. The demand for electricity varies with time as an installation can:
- work day but not at night
- work only working days and hours
- produce different products per day, hour or generally per period of time
- over-operate or sub-function according to the production needs of the products
- have different heating, air conditioning or lighting needs depending on the season
This oddity led to the use of the Total Demand Distortion (TDD) factor.
The difference of the TDD and THDi factors is in the denominator value.
The TDD has as denominator the maximum value of current of the installation instead of a random current.
In other words, the TDD calculates the harmonic distortion always in relation to the maximum operating current of the installation (fixed size) and not in the instantaneous operating current (constantly changing size) such as the THDi index.
The differences of the THD and TDD factors are described in detail in the world-famous article by T.Blooming & D. Carnovale.
When harmonics are measured, the purpose is to locate the maximum values of harmonics (see TDD) in the worst case scenario detection logic, which is why IEEE 519 refers to TDD (and not of the THDi factor).
How to measure the harmonic intensity measurements
After calculating the TDD values and determining the allowed harmonic intensity limits, the following should be done:
- Calculate the ratio of the current of the Transformer to the maximum current of the ISC / IL installation.
- Based on this and looking at the TDD table of IEEE 519, it is necessary to check at which value of the TDD (5%, 8%, 12%, 15% or 20%) corresponds.
Effects of wrong harmonic measurements
Conclusion:
Proper measurements, as well as appropriate technical training for the correct evaluation of measurement results, are essential prerequisites for addressing power quality problems in electrical installations.
So imagine the true harmonics of your installation to be 7% (with a 5% harmonic threshold based on the TDD index), and the measurements, because they are not done correctly, incorrectly show the value of 30% (based on the inappropriate THDi index) , which can also be done intentionally.
After installing the – most likely – inappropriate equipment, the final measurements show e.g. the 5% price, leading to the erroneous conclusion that your harmonics have dropped from 30% to 5%, while they have virtually dropped from 7% to 5%!
Until then, however, you have purchased, without real reason, expensive equipment to reduce your harmonics!
What is the final conclusion?
Without reliable complete measurements and accurate results, conclusions can not be properly drawn, while incorrect evaluation of the results, even if the measurements have been performed correctly, involves significant risks, such as:
- not to complete the recording of the installation sizes as a whole, but only a part of it, and thus to address the problem in part.
- to propose over-dimensioned and therefore more expensive or correspondingly sub-dimensional equipment than actual needs.
- not to correctly diagnose the nature of the problem and to propose inappropriate equipment (eg capacitors instead of filters, or filters instead of stabilizers).
- to give a false picture of the installation, resulting in the waste of money for unnecessary equipment.